The plastic pelletizing machine is the most important equipment in the plastic granulating line. The dehydrated plastic fragments enter the main machine of the pelletizer for heating and melting, and the melted plastic is extruded and drawn through the die head in the auxiliary machine to achieve granulation.
With a special screw design and different configurations, it is suitable for the production of PP, PE, PS, ABS, PVC, PC, and other plastics for regeneration and color-mixing granulation.
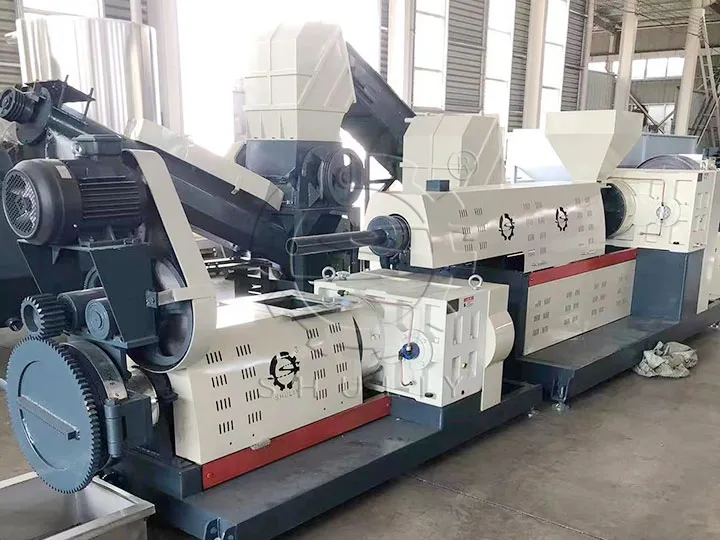
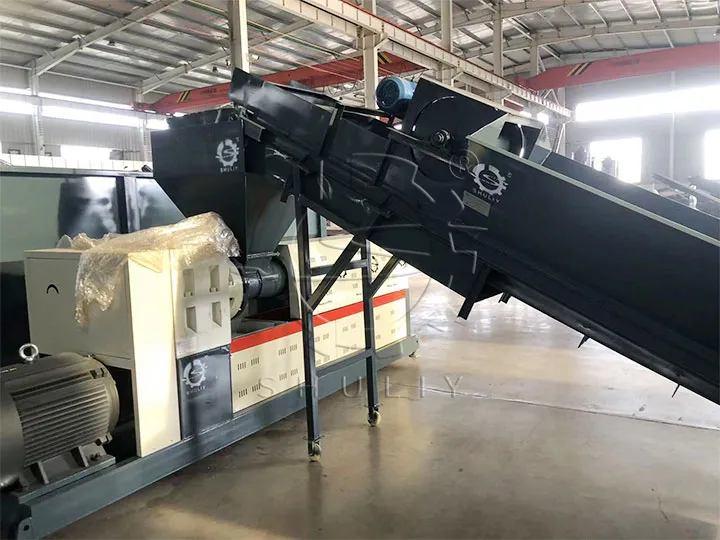
Introduction of Plastic Pelletizing Machine
The Plastic pelletizing machine consists of a main machine and a secondary machine. The main machine of the plastic granules making machine is the extruder, which consists of an extrusion system, transmission system, and heating and cooling system.
1, Extrusion system: The extrusion system includes screws, barrels, hoppers, heads, and mold heads. Plastic is plasticized into a uniform melt through the extrusion system and is continuously extruded by the screw head under the established pressure during this process.
2, Transmission system: The role of the transmission system is to drive the screw and supply the rotational speed required by the screw in the extrusion process, usually consisting of a motor, reducer, bearings, etc.
3, Heating and cooling device: Heating and cooling are necessary conditions for the plastic extrusion process to proceed.
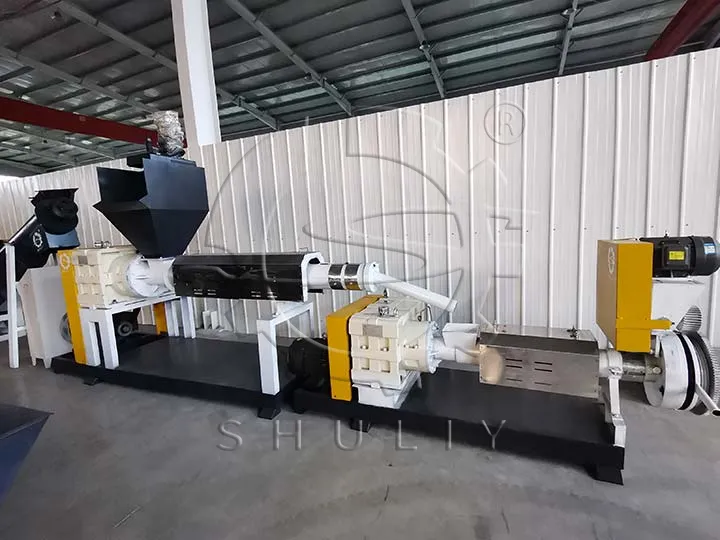
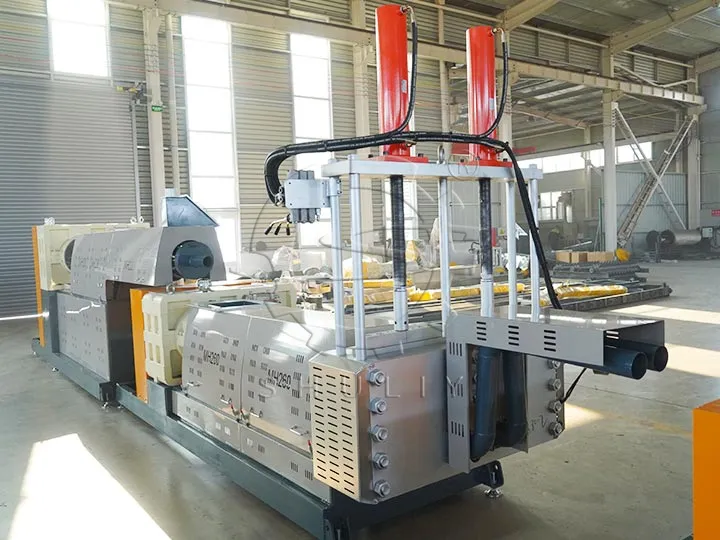
Advantages Of Recycling Granulator
Our recycled plastic extrusion machines offer some advantages to meet a variety of plastic recycling and production needs.
Wider Application
The pelletizer machine can efficiently process post-consumer plastic wastes and industrial trimmings to produce high-quality recycled plastic pellets, which are applied in injection molding, blow molding, extrusion, and other processes.
Various Granulating Methods
We offer two main types of pelletizing – strand pelletizing and water ring pelletizing. We recommend the appropriate method according to the customer’s raw material.
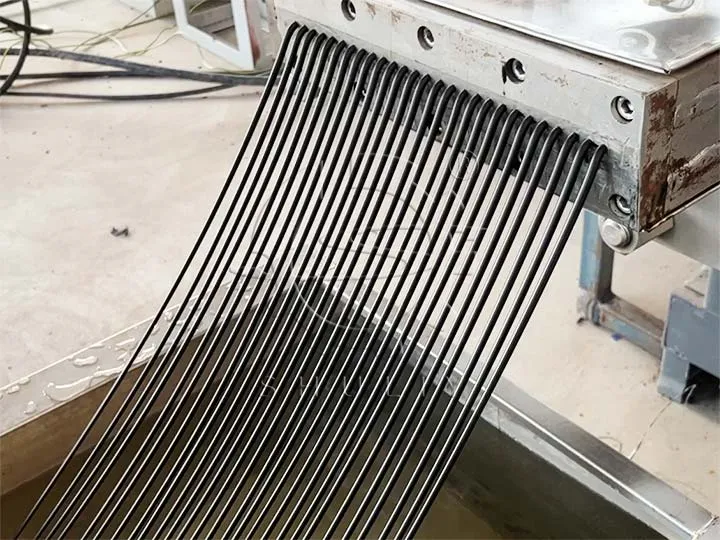
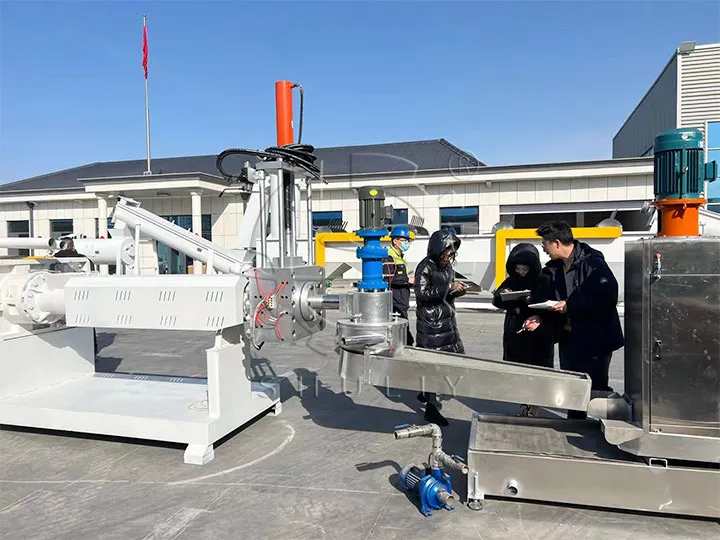
Extensive Optional Features
- Heating method: Electromagnetic heating, ceramic heating, heater ring.
- Die head: Electric gear die head, Hydraulic die head, Meshless slagging die head.
- Forced feeders: For lightweight materials, forced feeders can ensure uniform and stable feeding and improve production efficiency.
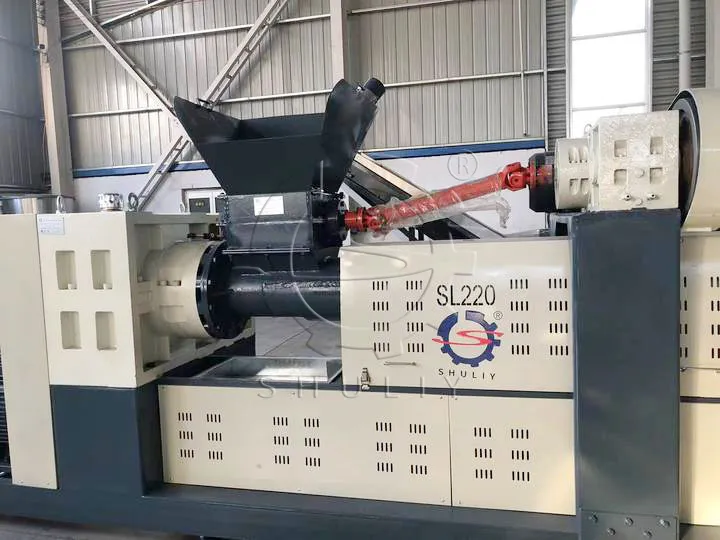
Wide Range of Models and Outputs
According to the customer’s production needs, we provide a variety of models of granulators, which can meet the production needs of different scales.
Application Scenarios of Plastic Granulating Equipment
Our pelletizer machine is widely used by plastic product manufacturers and plastic recycling factories.
Plastic Product Manufacturers
During the production of plastic products, the trimmings generated (such as film waste and injection molding waste) can be directly fed into the granulator for pelletizing. These unused post-industrial plastics can be regenerated into pellets and directly put into the production line for reuse, thus effectively saving costs.
Plastic Recycling Plants
Post-consumer recycled all kinds of plastic waste, including agricultural film, woven bags, nonwoven material, shrink wrap, stretch film, bubble wrap, laminated film, jumbo bags, food containers, appliance shells, bottle caps, drums, pipes, etc. can be pelletized after crushing and cleaning.
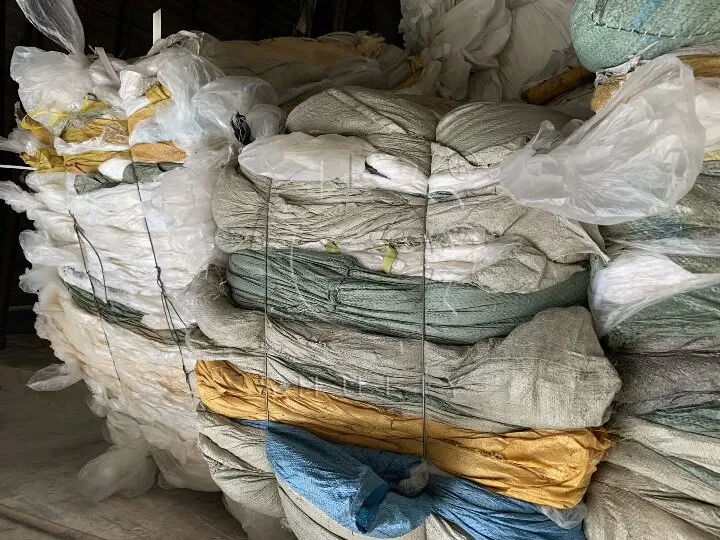
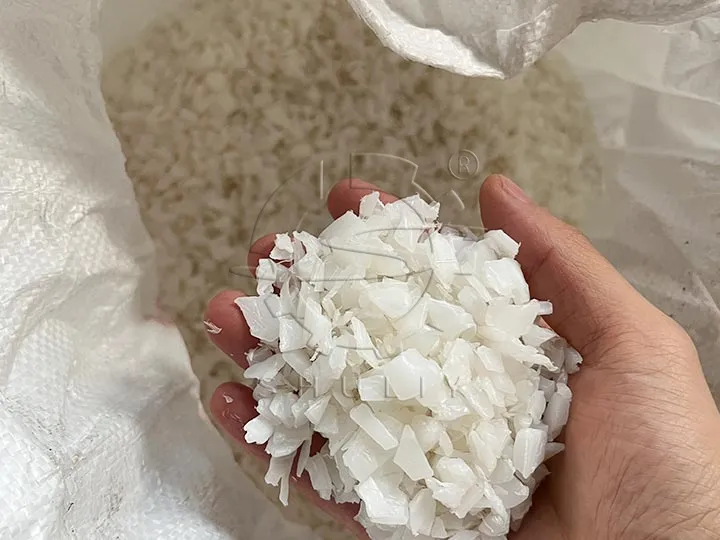
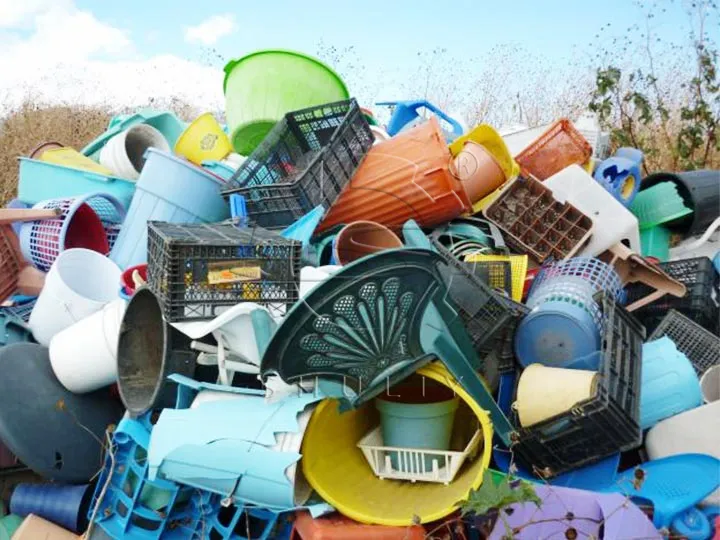
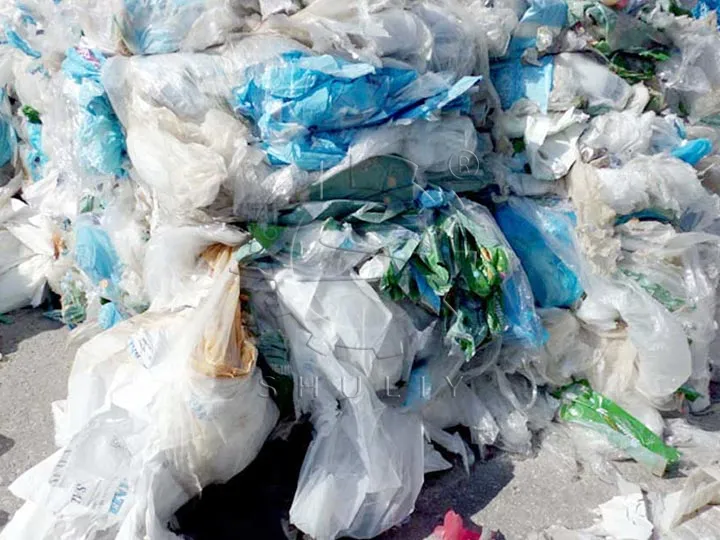
Structure of the Plastic Pellet Machine
This plastic pellet machine is mainly composed of a feeding port, screw press, reducer, heating device, press chamber, discharge port, mold head, machine body, base, motor, and other parts.
Two-stage tandem exhaust granulation unit is widely used in the recycling and granulation of various types of plastics such as LDPE, HDPE, PVC, PS, and PP.
The specially designed exhaust port can effectively remove the moisture and volatile gas generated during the melting process of the material, and the extruded particles are uniform, beautiful, and transparent, and the production efficiency is high. The main engine adapts to high-speed continuous operation.
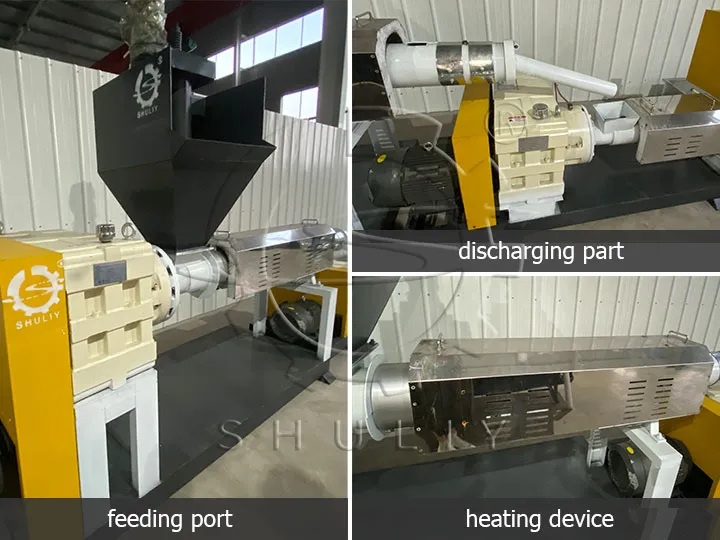
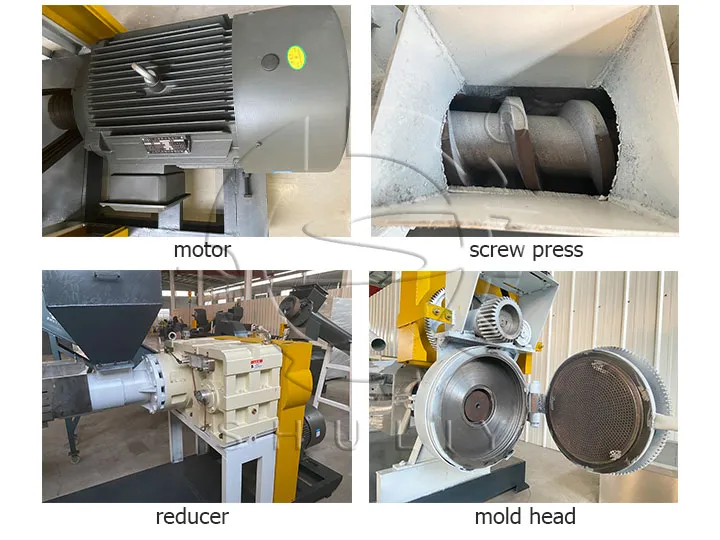
Plastic Granules Making Machine Show Video
Heating Method of Plastic Pelletizing Recycling Machine
The heating methods of plastic granulating equipment include electromagnetic heating, ceramic heating, quartz tube heating, and ordinary electric heating. Among them, electromagnetic heating has the best effect.
The pelletizing machine developed by Shuliy Machinery adopts the new technology of a high-frequency electromagnetic heater, which is energy-saving and efficient, accurate temperature control, safe, and reliable.
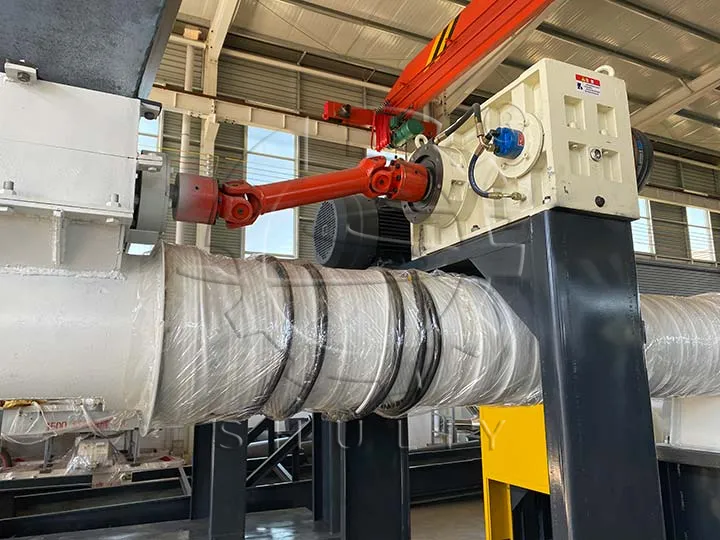
Electromagnetic heating: The outer wall of the material drum is wound with electromagnetic coils, with high power, internal heating, and an external insulation layer. Preheating time 10-15 minutes, energy saving 30-70% or more, long service life.
Ceramic heating: The outer layer has a decorative steel plate, and the nichrome alloy heating wire is sandwiched between the ceramics, which must be close to the sleeve. The power is 0.5~1.5 times higher than the ordinary one, the preheating time is 30-60 minutes, and the service life is slightly better.
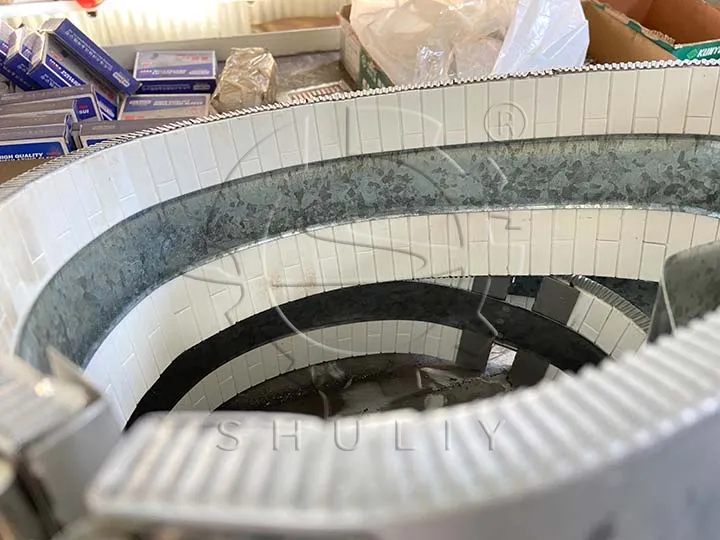
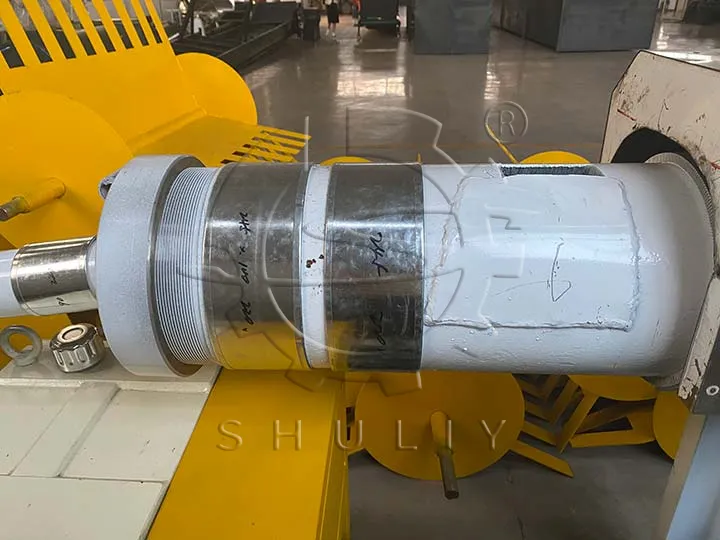
The mica heating ring is composed of high-quality nickel-chromium alloy heating wire as the heating element, using natural mica as the insulation layer, and the inner layer is made of galvanized/aluminum plate as the conductive heating layer. Moderate power, internal and external heat dissipation.
Mold Head of Plastic Granules Making Machine
The die heads of the plastic pelletizing machine are hydraulic die heads, electric gear die heads and meshless slagging die heads. The die head, also called the extrusion die head, is the molding part of the recycling granulator. Its function is to distribute the plastic melt from the barrel of the extruder well in the die head runner so that it can be extruded and molded from the die mouth at a uniform speed. The forming role of the extrusion die head is critical in the total extrusion process.
- Electric gear die head: An electric gear die head is a common plastic pelletizing machine die head, that is relatively simple and easy to operate and maintain. Suitable for small-scale plastic granule production, electric gear die heads have lower equipment costs compared to some more complex die heads.
- Hydraulic die head: Hydraulic die heads can achieve more precise extrusion control and are suitable for large-scale pellet production. The hydraulic system can provide a more stable extrusion process, helping to maintain consistent granule mass.
- Meshless slagging die head: The meshless slagging die head can effectively remove foreign objects and impurities during the plastic granulation process, improving plastic pellet quality. No need to shut down or change the network, improving production efficiency.
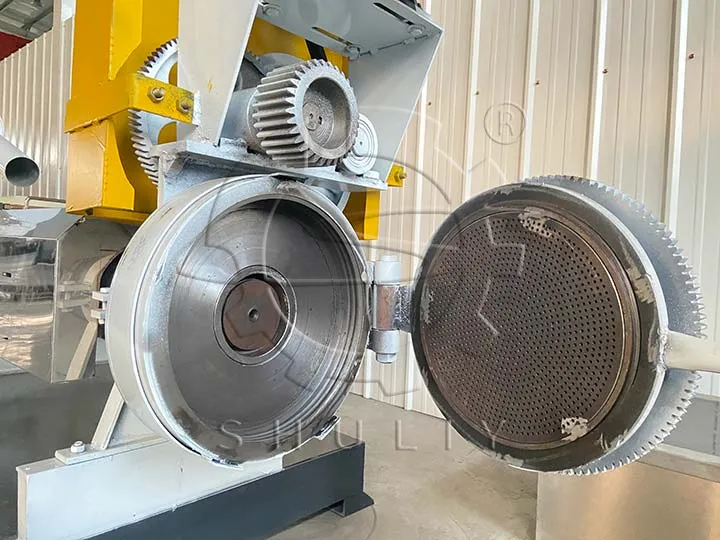
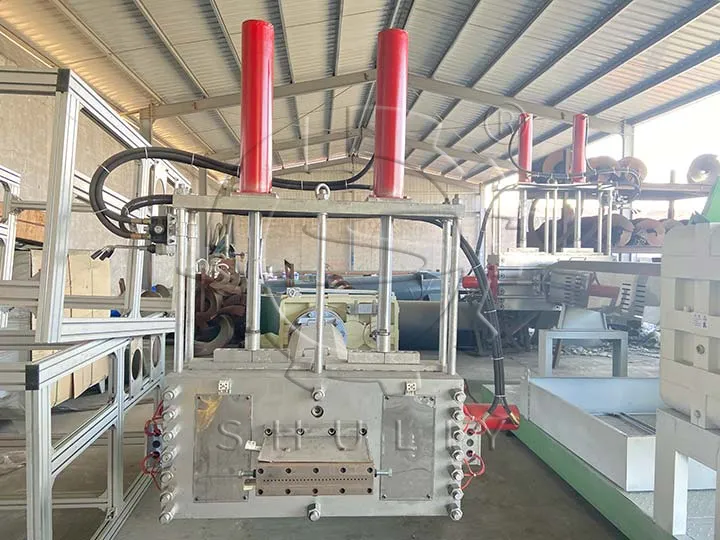
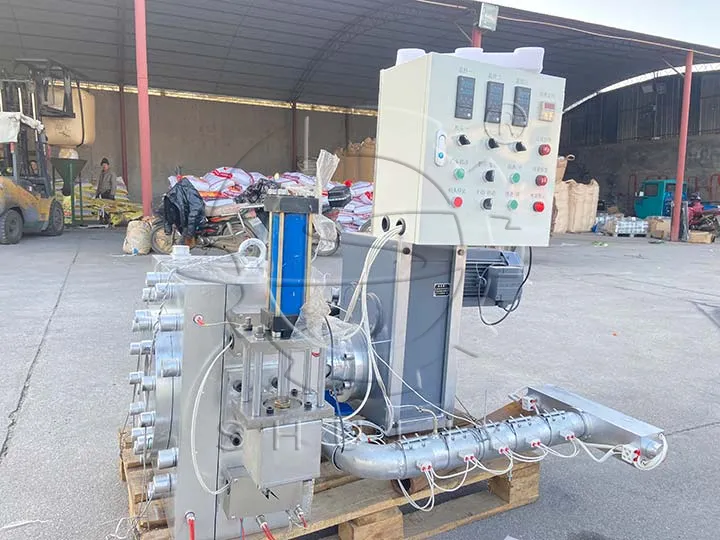
Video: How Does the Plastic Pelletizing Machine Work?
Parameters of Plastic Pelletizing Machine
Here is some parameter information of our granulator.
Output | 100-500kg/h |
Applicable Plastic Materials | PP HDPE LDPE LLDPE PVC ABS PS XPP BOPP EVA |
Applicable Material Sources | Post-consumer plastic recycling, post-industrial plastic recycling |
Pelletizing Methods | Strand pelletizing, water ring pelletizing |
Extruded Strip Size | 3-4mm |
Screws | Customizable lengths |
Optional Accessories | Heating method, die head, forced feeder |
Customizability | Customizable |
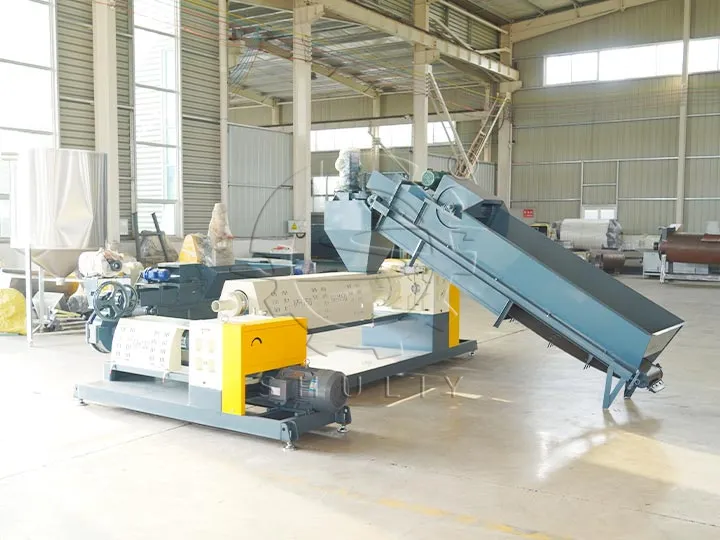
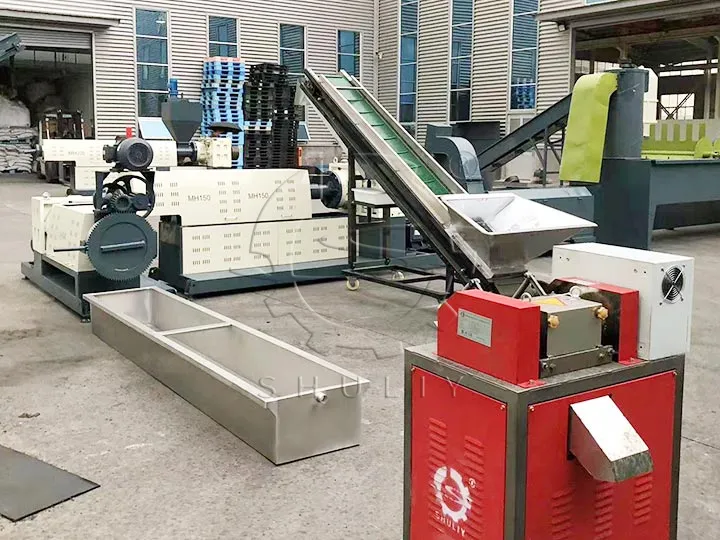
What Factors Affect the Price of Plastic Pelletizing Machines?
- Models and specifications: Different models and specifications of the plastic granule machine have different processing capacities and functions, and the price will vary accordingly.
- Brands and manufacturers: Well-known brands and specialized manufacturers usually provide more reliable equipment and after-sales service, but their prices may be relatively high.
- Materials and workmanship: The materials and workmanship used in the manufacture of a plastic pelletizer machine will affect its durability and performance. High-quality materials and workmanship usually increase the price.
- Degree of automation: The plastic granulator with more automation is usually more expensive. Automation features can increase productivity, but they can also increase the cost of the equipment.
Successful Cases of Plastic Granulator
HDPE Pelletizing Machine Applied in Nigeria
Our Nigerian customer bought an HDPE pelletizing machine from Shuliy Machinery, and this machine has been successfully installed and applied.
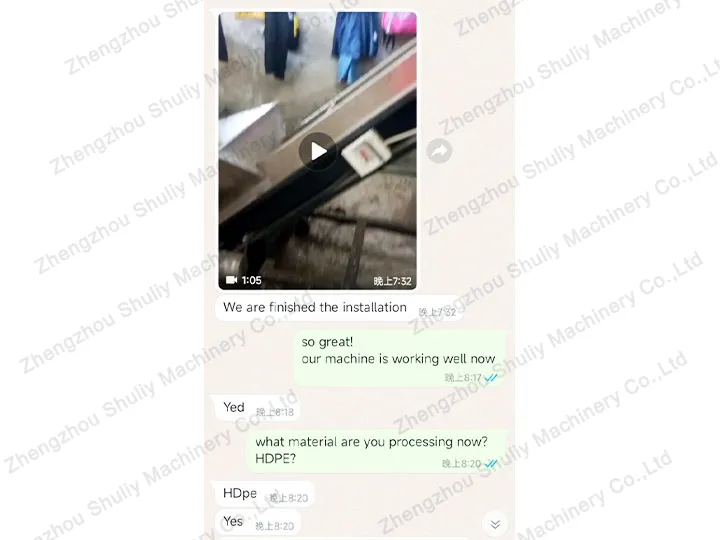
Shuliy Plastics Granulator Running in Mozambique
The plastics granulator shipped to Mozambique is running well and the customer is very happy with our machine, sharing a video of the machine in operation with Shuliy Group.
Choose One Complete Plastic Recycling Line
The PP PE granule extruder is used to melt plastic fragments and extrude them into strips. The plastic waste extruder machine is the core equipment in the plastic granulation line, and Shuliy Machinery can provide our customers with complete plastic recycling production line equipment.
The important equipment of the plastic recycling line includes a plastic crusher, plastic washing tank, plastic pelletizing recycling machine, cooling tank, and pellet cutting machine. We can also provide customized granulation lines according to customer needs.

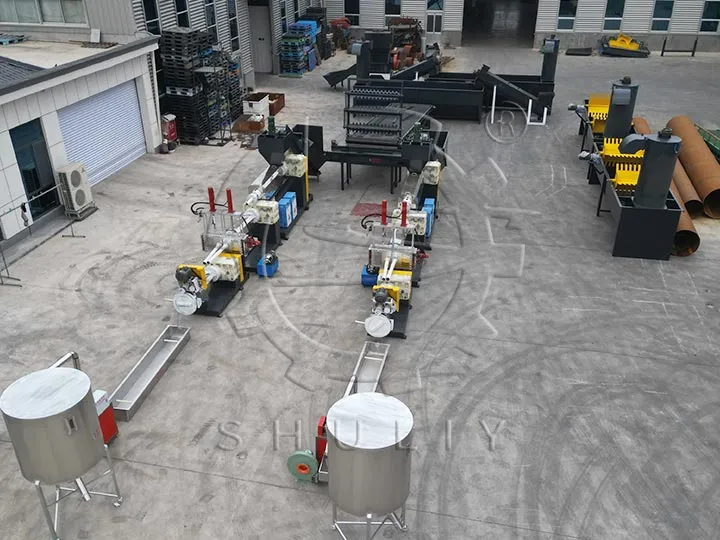