PET bottle recycling washing line is used to separate non-PET materials such as caps, labels, and other non-PET materials from baled waste plastic bottles, then crushed, cleaned, and processed into clean recycled PET bottle flakes. The recycled bottle flakes can be made into recycled pellets for the manufacture of other PET products or sold to chemical fiber manufacturers.
PET Bottle Recycling Washing Line Description
PET bottle recycling washing line consists of a range of plastic recycling machinery including a PET label remover machine, plastic bottle shredder, PP PE separating tank, PET bottle flakes hot washing machine, friction washer, and plastic dewatering machine. We have a standard PET bottle recycling washing line with outputs ranging from 500kg/h to 6000kg/h, and we can also customize a PET bottle recycling line to suit your needs and output.
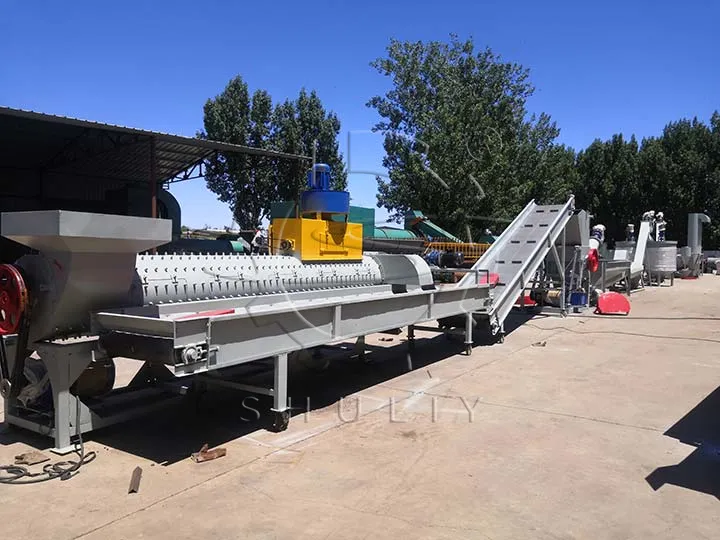
Working Processes of PET Bottle Recycling Line
- Bale opener: Breaks up plastic bales that have been compacted into cubes.
- Tumbler sieve: It is a rotating cylinder with a screen that sifts out impurities such as stones, sediment, or glass.
- PET label remover machine: Numerous blades inside to disengage the PVC labels from plastic bottles.
- Plastic bottle shredder: The plastic bottle shredder crushes PET bottles into uniformly sized pieces.
- PP PE separating tank: Use the buoyancy of the water to separate the bottle piece from the cap. Labels and PP/PE plastic bottle caps will float, while PET plastic flakes will sink.
- PET bottle flakes hot washing machine: It removes adhesive from labels and oil residues. Hot water can dissolve the adhesive on the bottle, and many stains that are hard to remove with cold water can be removed. Detergents can also be added for better washing results.
- Friction washer: By high-speed friction between the rotating shaft and the water flow, the dirt and impurities on the PET bottle sheet are effectively removed.
- Plastic dewatering machine: Highly efficient dewatering to evaporate water from the surface of PET sheets.