A customer who has purchased our EPS granulator has asked how to maintain the machine. In this article, we will answer the customer’s question and explore how to maintain the plastic foam granulator.
As the core equipment in an EPS foam granulating line, the plastic foam granulator plays a crucial role in the expanded polystyrene (EPS) foam manufacturing process. To ensure production efficiency and product quality, proper maintenance measures are essential for the smooth operation of the EPS pelletizing machine.
Application of EPS Granulator in Plastic Foam Pelletizing Line
The EPS granulator is a primary component of an EPS foam granulating line. It is utilized to melt EPS raw material, extrude the molten EPS through a screw, and transform it into small pellets through a plastic granule cutter. These pellets are subsequently used in the production of insulation materials, packaging materials, and more.

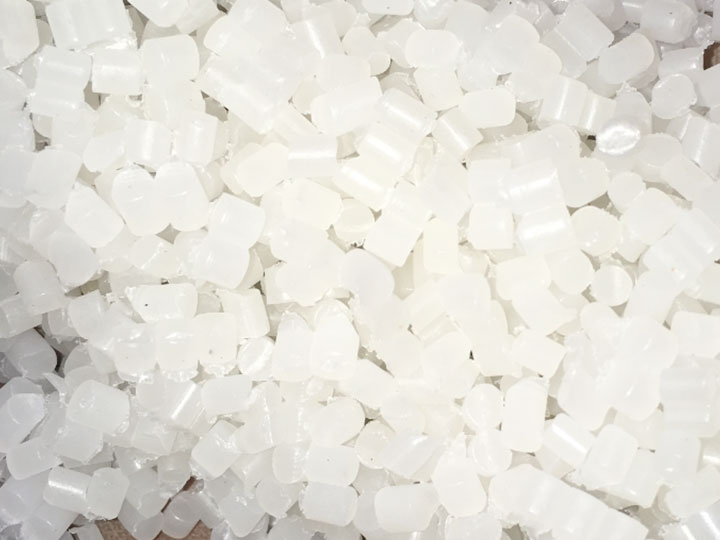
The Importance of Maintaining Plastic Foam Granulator
Maintaining the EPS granulator not only enhances production efficiency but also ensures the production of high-quality foam pellets. The following are key steps in maintaining the EPS pelletizing machine:
- Regular Cleaning: Regularly clean the EPS granulator’s feed inlet, discharge outlet, screw, and other parts to prevent residue buildup that could affect production and pellet quality.
- Lubrication Maintenance: Conduct routine checks and maintenance on the lubrication system of the EPS pelletizing machine to ensure the smooth operation of moving components.
- Component Replacement: Based on usage frequency and manufacturer recommendations, regularly inspect vulnerable components such as blades and screen meshes. Replace worn components promptly to prevent any impact on pellet quality.
- Electrical System Inspection: Periodically inspect electrical circuits, control panels, and other electrical components to ensure safety and reliability, and to prevent malfunctions.
- Operator Training: Provide specialized training to operators to ensure they understand the correct operating procedures and maintenance requirements, thereby reducing the risks associated with operational errors.
- Maintenance Records: Maintain detailed maintenance records including dates, tasks performed, and usage status. This aids in tracking maintenance history and making informed scheduling decisions.