The PET flakes washing and sorting tank is a specialized equipment for material separation in the plastic recycling process. It effectively separates light impurities such as bottle caps and labels from heavy PET bottle flakes through the buoyancy of water and the difference in density of materials.
The equipment is easy to operate and ensures that plastics such as PET bottle flakes get a higher purity during the cleaning process, which is a key part of improving the quality of recycled materials. Whether used in the washing line of PET flakes or other plastics processing lines, sink float separation tanks provide efficient and reliable separation.
Working Principle Of Sink Float Separation Tank
The sink float separation tank utilizes water as a medium and relies on the density difference between different plastics to achieve an effective separation process. It is mainly applied to separate PET bottle flakes from PP, PE bottle caps, or labels.
PET bottle flakes, due to their higher density, sink to the bottom of the tank and are transported to the next process via a screw conveyor at the bottom. In contrast, the less dense bottle caps and residual labels float on the surface of the water. The caps and labels floating on the water surface are guided to the discharge outlet next to the baffle plate at the back of the tank, where they are discharged, thus realizing efficient separation.
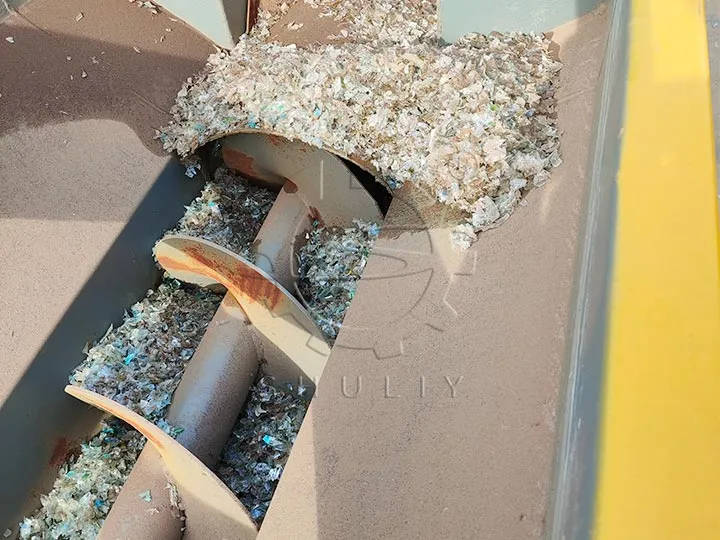
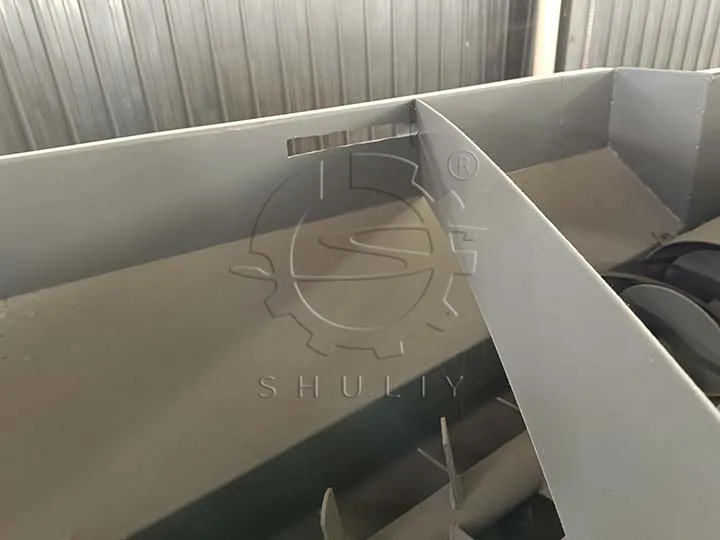
Features of Sink Float Plastic Separation
- The sink float separation tank is made of stainless steel.
- Internal blade thickness 6mm, both sides of the outer wall 8mm.
- The twin-screw floating chute is recommended for output greater than 2 tons, with 4 mm outer wall thickness 6 mm blades, and removable bottom height.
- The machine can be customized according to customer requirements.
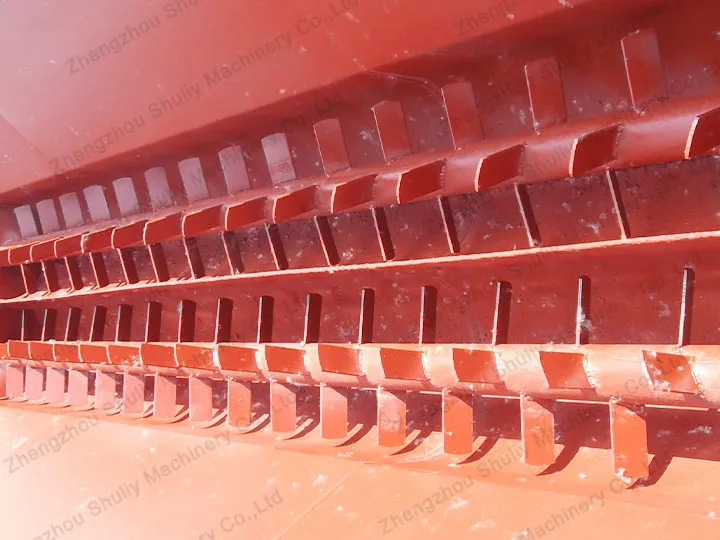
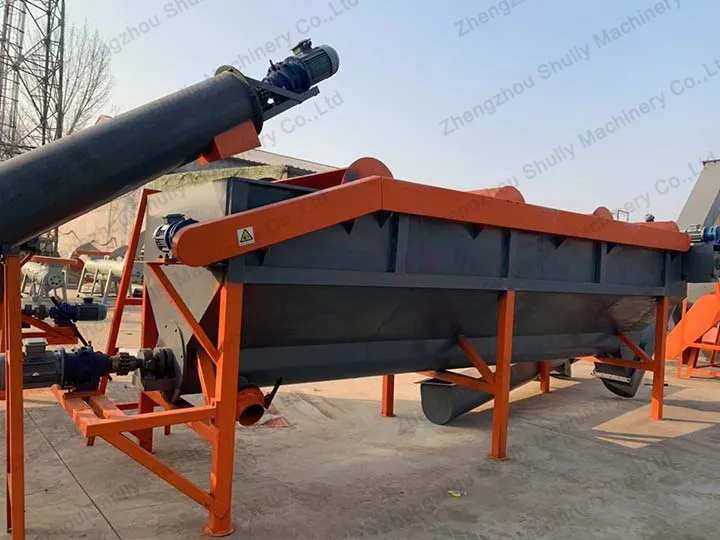
Why Do You Need A Washing and Sorting Tank?
Most of the cold drink bottles are made of PET plastic, which is 100% recyclable material. PET flakes with high native content can be recycled to make new products such as filament, staple fiber, clothing, packing tape, etc. PET flakes can also be made into pellets for recycling.
The cap is made of PP or PE, so the cap needs to be detached through the sink float separation tank to get a single content of PET plastic flakes. This machine is widely used in PET bottle washing plants.
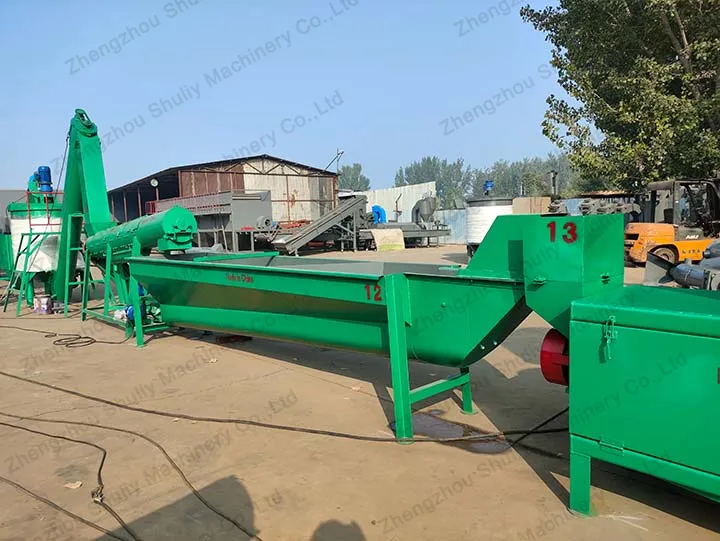
Number of Washing and Sorting Tank Installations
The number of sink float separation tanks that need to be installed in a PET flakes washing line depends on the degree of soiling of the material and the throughput. If the material is dirty or the quality of the final product is high, you can consider installing one or two more separator tanks before the plastic dewatering machine.
From the production point of view, if the output is small, usually need to install 1 or 2 units; if the output is 1 ton per hour, it is recommended to install 3 units; and for a larger output, such as 3 tons per hour, it may be necessary to install 4 sets of washing and sorting tanks.
The first sink float separation tank is usually installed after the bottle crusher machine, the main function is to separate the caps and labels from the PET bottle flakes. After the hot washing tank, one or two washing and sorting tanks are usually installed, which can not only separate the residual impurities again but also effectively wash out the lye brought out from the hot washing tank, reduce the pH value to below 8, to improve the cleanliness of PET bottle flakes.
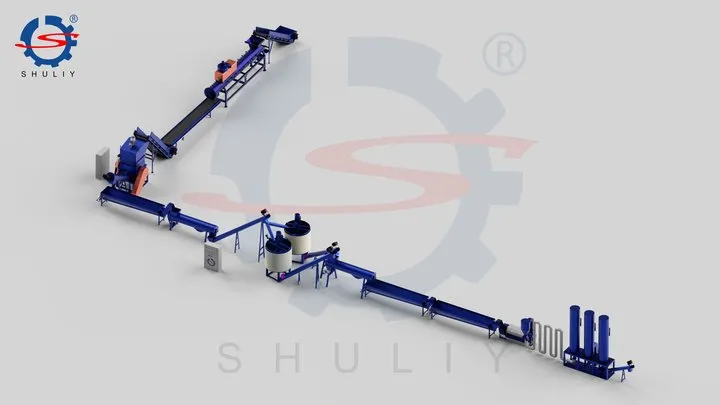
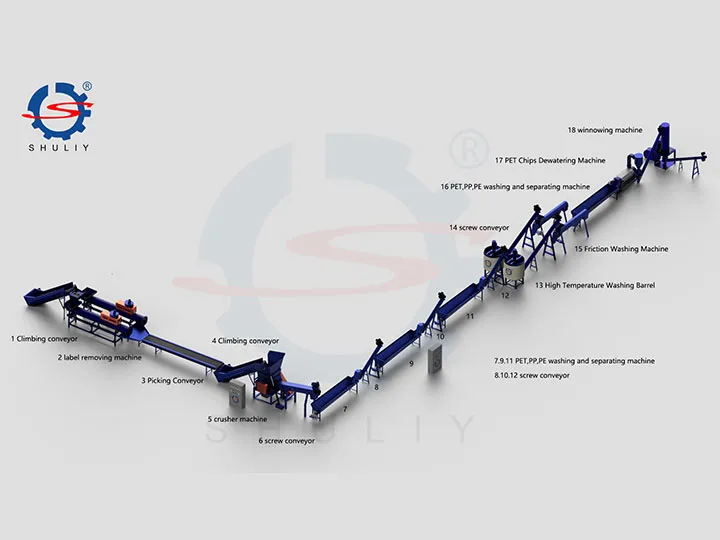
Global Cases of Plastic Float Sink Tank
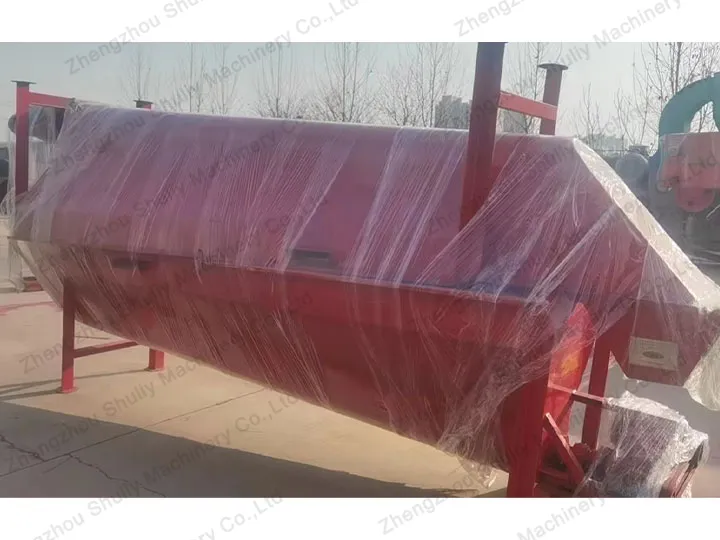
